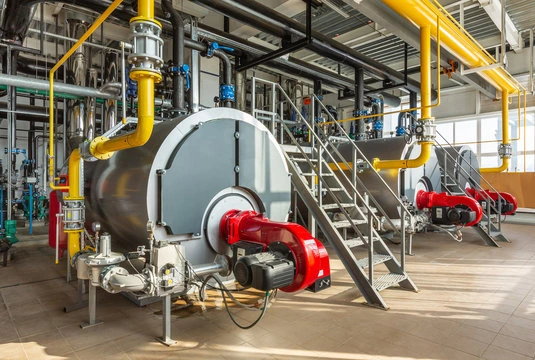
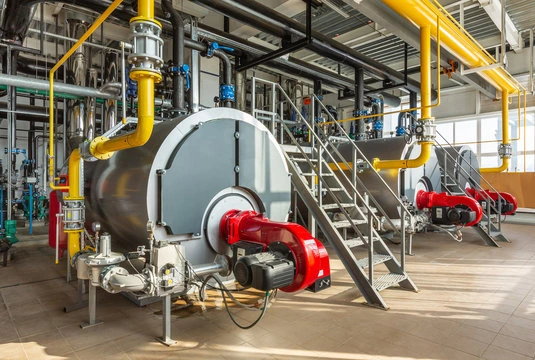
ETP Installation
400+
Waste Water Treated Per Day
70 MLD
Inhouse Manufacturing
Yes
Mega Project
45 MLD ETP at L&T Ludhiana
Effluent Treatment Plant – ETP for Oil and Gas Industry
Capacity | Variable, tailored to the specific needs of oil and gas facilities. |
Treatment Technique | Multi-stage process including physical, chemical, and biological treatment. |
Inlet Flow Rate | Customizable based on site requirements and wastewater characteristics. |
Water Source | Various sources including produced water, drilling fluids, and refinery effluents. |
Automation Grade | Highly automated systems for efficient operation and monitoring. |
Operation & Maintenance Support | Comprehensive support including routine maintenance and troubleshooting. |
Industry We Serve | Oil and gas exploration, production, refining, and petrochemicals. |
Turnkey Project with Civil | Available, ensuring seamless integration with existing infrastructure. |
Government Compliances & Approval | Compliance with local regulations and environmental standards. |
Customized Solutions :Tailored to handle diverse wastewater streams generated throughout the oil and gas value chain.
Advanced Treatment Technologies :Incorporates state-of-the-art processes to address complex contaminants such as hydrocarbons, heavy metals, and dissolved solids.
Modular Design : Scalable and modular systems to accommodate fluctuating flow rates and evolving treatment needs.
Effluent Reuse Potential :Provides opportunities for treated effluent reuse in non-potable applications, reducing freshwater consumption.
Resource Recovery : Implements processes for the recovery of valuable resources from wastewater, such as oil, chemicals, and energy.
Robust Monitoring and Control :Advanced control systems and real-time monitoring ensure optimal performance and regulatory compliance.
Emergency Response Capability :Built-in redundancy and emergency protocols to handle unexpected events and ensure uninterrupted operation.
Environmental Compliance : Ensures compliance with stringent environmental regulations and standards, mitigating the risk of fines and penalties.
Cost-Effective Solutions :Maximizes efficiency and minimizes operational costs through optimized treatment processes and resource recovery.
Expertise and Support :Backed by a team of experienced engineers and technicians providing ongoing support and expertise.
At the heart of our ETP is a multi-stage treatment process that combines advanced physical, chemical, and biological techniques to effectively remove contaminants from wastewater. Whether it's produced water from oil wells, drilling fluids from exploration activities, or refinery effluents from petrochemical plants, our tailored solutions are capable of handling a wide range of pollutants, including hydrocarbons, heavy metals, and dissolved solids.
Our ETP systems are highly adaptable, with customizable capacities and flow rates to meet the specific needs of each oil and gas facility. Whether it's a small-scale operation or a large refinery complex, our modular design allows for seamless integration and expansion as production volumes fluctuate and treatment requirements evolve.
In addition to regulatory compliance and environmental stewardship, our ETP emphasizes resource recovery and efficiency. By implementing advanced treatment technologies and process optimization strategies, we maximize the recovery of valuable resources from wastewater, including oil, chemicals, and energy. This not only reduces operational costs but also minimizes the environmental impact of oil and gas operations.
With robust monitoring and control systems, our ETP ensures continuous operation and performance optimization, even in the face of unexpected events or emergencies. Our team of experts provides comprehensive support, including routine maintenance, troubleshooting, and emergency response, to ensure the reliability and efficiency of our ETP systems.
In conclusion, the Effluent Treatment Plant for the Oil and Gas Industry embodies our commitment to innovation, sustainability, and operational excellence. By providing customized solutions tailored to the unique needs of oil and gas facilities, we help our clients meet regulatory requirements, minimize environmental impact, and maximize resource recovery, ensuring a cleaner, greener future for the industry.
customer testimonials
Our oil and gas facility has benefited immensely from the ETP solution provided by Awetech Works. It's been instrumental in ensuring regulatory compliance and environmental responsibility.
Why Effluent Should Be Treated for Oil and Gas Industry
Effluent treatment is a crucial aspect of responsible environmental management in the oil and gas industry. Here are additional reasons why effluent should be treated
1.Environmental Protection:
Untreated effluent from oil and gas operations can contain various pollutants, including hydrocarbons, heavy metals, and toxic chemicals. Discharging such contaminants into the environment can lead to soil and water contamination, endangering ecosystems and public health. Treating effluent before discharge helps minimize environmental impact and protects natural resources.
2.Regulatory Compliance:
Oil and gas facilities are subject to stringent environmental regulations governing wastewater discharge and pollution control. Compliance with these regulations, such as the Clean Water Act (CWA) and the Resource Conservation and Recovery Act (RCRA), is essential to avoid fines, penalties, and legal liabilities. Effluent treatment ensures that facilities meet regulatory requirements and demonstrate their commitment to environmental responsibility.
3.Protection of Water Resources:
Wastewater from oil and gas operations often contains pollutants that can contaminate water bodies, posing risks to aquatic life and human health. Treating effluent removes harmful substances, ensuring the protection of freshwater resources for drinking, irrigation, and recreational use. Clean water is essential for sustaining ecosystems and supporting communities, making effluent treatment a vital priority.
4.Public Health and Safety:
Untreated effluent may contain hazardous substances and pathogens that can pose risks to public health and safety. By treating effluent to remove contaminants and disinfect pathogens, oil and gas facilities protect the health and well-being of workers, nearby communities, and ecosystems. Effluent treatment minimizes the spread of waterborne diseases and reduces the risk of exposure to harmful chemicals.
5.Corporate Responsibility:
As environmental awareness grows, stakeholders increasingly expect oil and gas companies to demonstrate responsible environmental stewardship. Investing in effluent treatment reflects a commitment to sustainability, corporate social responsibility (CSR), and ethical business practices. By prioritizing effluent treatment, companies enhance their reputation, build trust with stakeholders, and contribute to a more sustainable future.
6.Operational Efficiency:
Efficient effluent treatment systems not only protect the environment but also improve operational efficiency and cost-effectiveness for oil and gas facilities. By recovering valuable resources from treated wastewater, such as water, hydrocarbons, and minerals, facilities reduce their reliance on freshwater sources, lower disposal costs, and generate additional revenue streams. Effluent treatment enhances operational sustainability and financial performance.
Effluent Treatment Plant (ETP) Process for Oil and Gas Industry
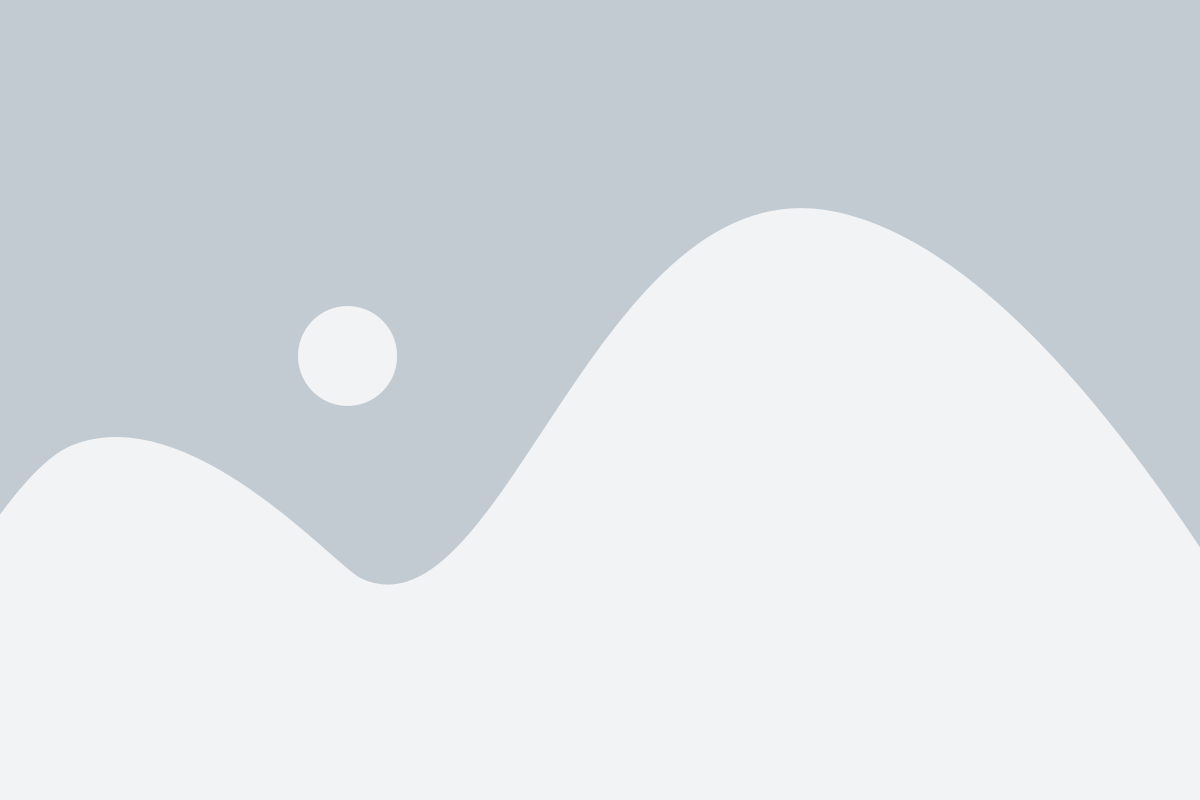
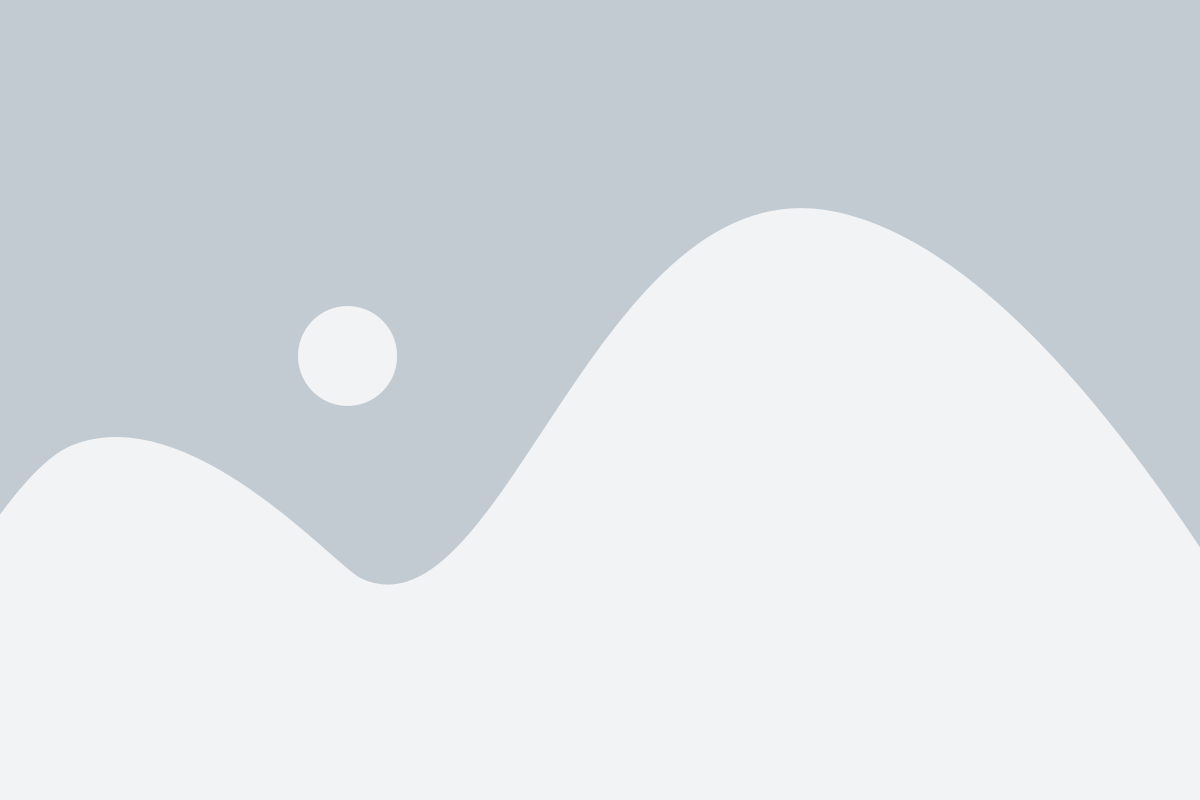
Effluent Treatment Plant (ETP) Process for the Oil and Gas Industry encompasses a comprehensive approach to managing and treating wastewater streams generated throughout the oil and gas value chain. From upstream exploration and production activities to downstream refining and petrochemical processes, the ETP process addresses the diverse and complex contaminants present in oil and gas wastewater, ensuring compliance with environmental regulations and industry standards.
1.Inlet Reception and Screening:
The process begins with the reception of wastewater from various sources within the oil and gas facility, including produced water, drilling fluids, and refinery effluents. The wastewater undergoes preliminary screening to remove coarse solids, debris, and large particles, preventing them from entering downstream treatment units.
2.Oil-Water Separation:
Following screening, the wastewater enters the oil-water separation unit, where hydrocarbons and other oily contaminants are separated from the aqueous phase. This process typically involves gravity-based separation techniques such as API separators or induced gas flotation (IGF) units, which facilitate the removal of free and emulsified oil from the wastewater stream.
3.Chemical Treatment:
After oil-water separation, the wastewater undergoes chemical treatment to further remove dissolved and suspended contaminants. Chemical additives such as coagulants, flocculants, and demulsifiers are added to the wastewater to promote the aggregation and precipitation of fine particles, colloids, and dissolved solids, facilitating their removal through sedimentation or filtration.
4.Biological Treatment:
Following chemical treatment, the wastewater enters the biological treatment unit, where organic contaminants are biologically degraded by microorganisms under aerobic or anaerobic conditions. Biological reactors such as activated sludge systems, sequencing batch reactors (SBRs), or anaerobic digesters provide an ideal environment for microbial growth and metabolic activity, resulting in the reduction of biochemical oxygen demand (BOD), chemical oxygen demand (COD), and other organic pollutants.
5.Advanced Treatment Processes:
In some cases, additional treatment processes may be required to meet stringent discharge standards or address specific contaminants present in the wastewater. Advanced treatment technologies such as membrane filtration, activated carbon adsorption, and advanced oxidation processes (AOPs) may be employed to further polish the effluent and remove residual contaminants, including trace organic compounds, heavy metals, and pathogens.
6.Tertiary Treatment and Disinfection:
The treated wastewater undergoes tertiary treatment to ensure compliance with regulatory requirements and environmental standards. This may involve additional filtration, disinfection, or chemical treatment to remove remaining contaminants and pathogens from the effluent. Common disinfection methods include chlorination, ultraviolet (UV) irradiation, ozone treatment, or advanced oxidation, depending on the specific requirements and discharge regulations.
7.Effluent Monitoring and Quality Assurance:
Throughout the treatment process, effluent quality is continuously monitored to ensure compliance with regulatory standards and discharge limits. Advanced sensors and instrumentation provide real-time data on key parameters such as pH, turbidity, dissolved oxygen, and chemical concentrations, allowing for precise control and adjustment of treatment processes to optimize performance and efficiency.
8.Effluent Reuse and Resource Recovery:
Treated effluent from the ETP may be suitable for reuse in various non-potable applications within the oil and gas facility, such as cooling water, boiler feed, or irrigation. Effluent reuse not only conserves freshwater resources but also reduces wastewater discharge volumes and environmental impact. Additionally, the ETP process may facilitate the recovery of valuable resources from wastewater, such as oil, chemicals, and nutrients, through specialized recovery technologies and processes.
9.Sludge Management and Disposal:
Sludge generated during the treatment process, including sedimentation and biological solids, is dewatered, stabilized, and disposed of in accordance with regulatory requirements and best practices. Sludge management may involve dewatering processes such as centrifugation, filtration, or mechanical dewatering, followed by appropriate treatment or disposal methods such as landfilling, incineration, or beneficial reuse.
10.Continuous Optimization and Performance Monitoring:
The operation of the ETP is continuously optimized through regular performance monitoring, process control adjustments, and preventive maintenance activities. Routine inspections, equipment calibration, and laboratory analysis ensure the reliability, efficiency, and regulatory compliance of the treatment system, minimizing downtime and operational risks.
Frequently Asked Questions [FAQ]
An ETP is a specialized facility designed to treat wastewater generated during various oil and gas operations, such as drilling, production, refining, and petrochemical processes.
Effluent treatment is crucial for minimizing environmental pollution and ensuring compliance with regulatory standards by removing contaminants from wastewater before discharge.
Wastewater sources include produced water, hydraulic fracturing flowback, drilling muds, cooling water, refinery effluents, and process water from petrochemical plants.
The ETP employs various treatment processes such as sedimentation, filtration, and chemical treatment to remove contaminants like oil, grease, and dissolved solids from produced water.
Treatment methods may include filtration, sedimentation, chemical oxidation, and advanced processes like reverse osmosis to remove suspended solids, dissolved chemicals, and organic compounds.
Yes, ETPs can be designed to accommodate the unique challenges of offshore operations, including space limitations, harsh environmental conditions, and strict discharge regulations.
The ETP utilizes advanced monitoring systems, process controls, and treatment technologies to meet regulatory requirements and maintain effluent quality within permissible limits.
Yes, ETPs are equipped with adjustable treatment processes and capacity buffers to accommodate variations in flow rates and wastewater characteristics.
ETPs incorporate safety features such as leak detection systems, emergency shutdown mechanisms, and secondary containment to prevent accidents and mitigate risks to personnel and the environment.
Specialized treatment processes such as air stripping, activated carbon adsorption, and chemical oxidation are employed to remove hazardous substances and VOCs from wastewater.
Yes, the ETP can be tailored to handle wastewater from secondary recovery methods like water flooding and tertiary methods like steam injection or chemical flooding, employing appropriate treatment techniques.
The ETP treats drilling muds and cuttings by separating solids, recovering drilling fluids for reuse, and stabilizing or detoxifying residual wastes before disposal to reduce environmental contamination.
The ETP employs a combination of physical, chemical, and biological treatment processes to remove contaminants such as oil, grease, heavy metals, and organic compounds from refinery and petrochemical wastewater.
The ETP implements water recycling and reuse programs, utilizing treated wastewater for non-potable purposes such as irrigation, dust control, and secondary recovery operations to conserve freshwater resources.
Yes, the ETP employs specialized treatment methods such as chemical oxidation, air stripping, and biological processes to remove hydrogen sulfide and other corrosive gases from wastewater.
The ETP may employ techniques like aeration, degasification, or membrane separation to remove dissolved gases from wastewater, depending on the specific gas composition and treatment requirements.
The ETP incorporates odor control systems such as biofilters, activated carbon adsorption, and chemical scrubbers to mitigate odor emissions from wastewater treatment processes.
Treated wastewater may be discharged into receiving water bodies or reused for beneficial purposes, while sludge and brine are dewatered, stabilized, and disposed of in compliance with regulatory requirements.
Yes, ETPs can be modified, upgraded, or expanded to meet evolving regulatory standards, operational demands, and technological advancements through retrofitting or additional treatment units.
The ETP utilizes a combination of online analyzers, sensors, data loggers, and control algorithms to continuously monitor key parameters such as flow rates, pH, dissolved oxygen, turbidity, and chemical concentrations, enabling real-time adjustments and ensuring regulatory compliance.
Join Over +15,000 Happy Clients!


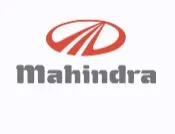
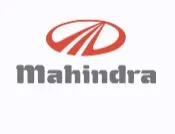




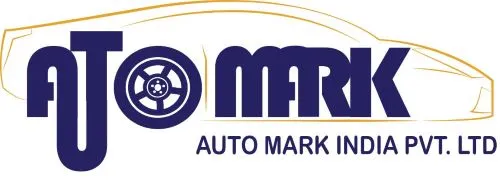
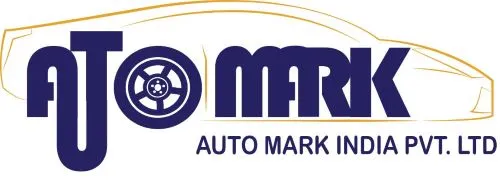


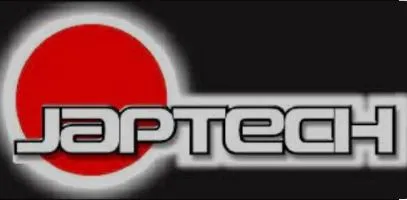
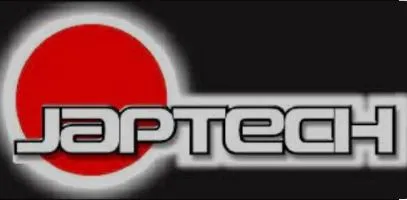
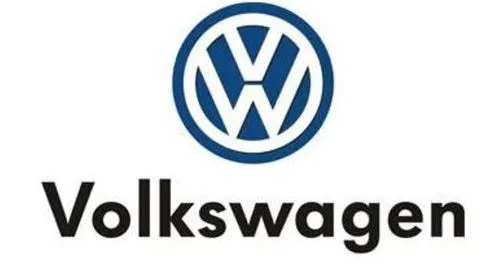
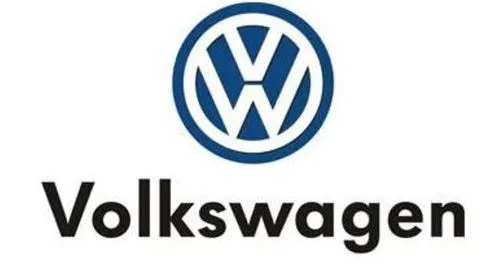




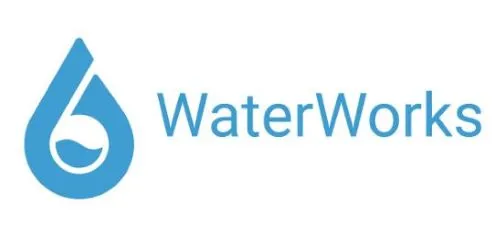
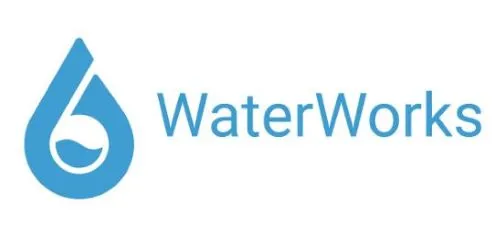


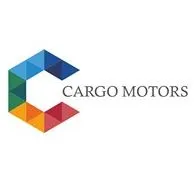
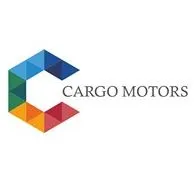






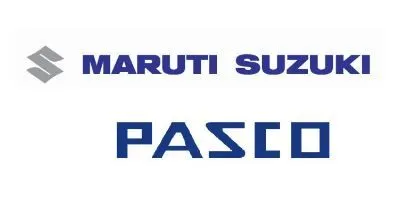
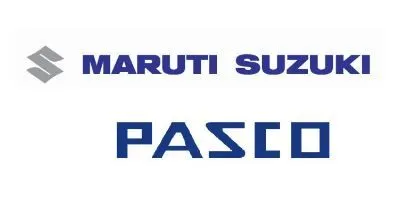
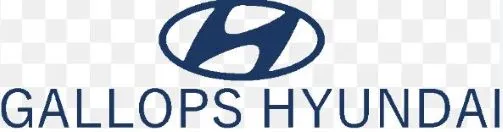
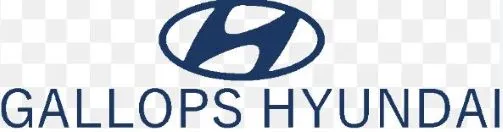






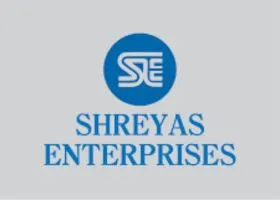
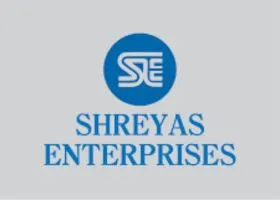
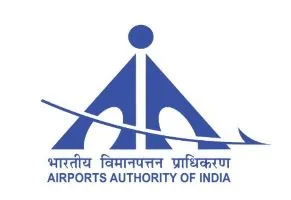
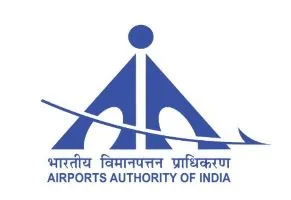
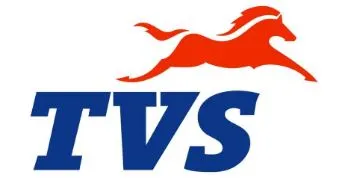
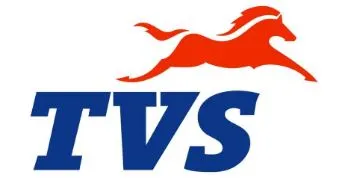










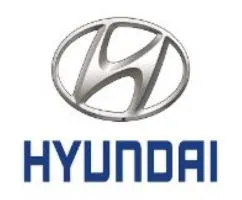
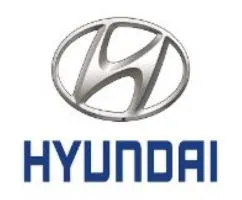
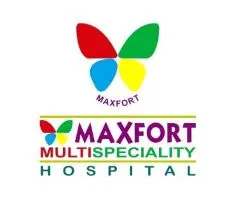
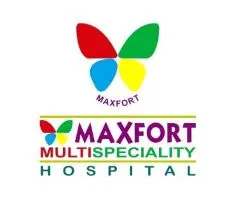


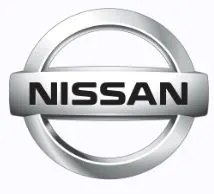
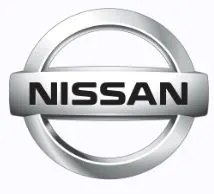
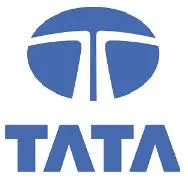
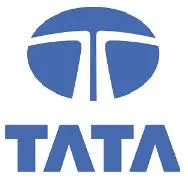


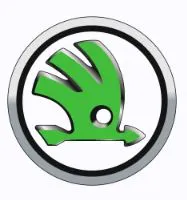
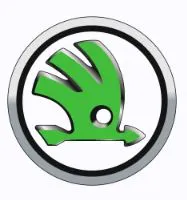
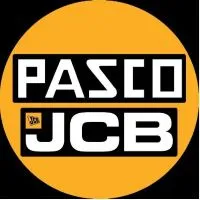
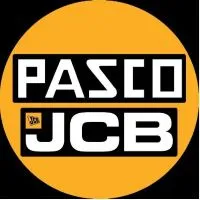




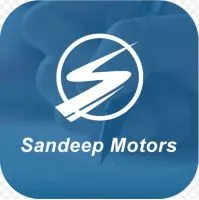
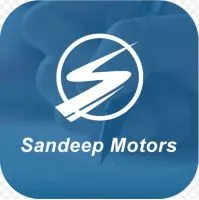


Salient Features
Concept to Commissioning
In-house team for Design. Engineering, Martufacturing, Execution and Service support gives full control over project ownership and quality
Experienced Team
Entire team possess average Industrial Experience of 7+ Year and have proven track record
Tailor Made Solutions
Our wide experience of solution design in multiple technologies enable us to choose technology that is most economical and efficient in long run.
Future Ready Products
Automation is the heart of every Awetech product. Our products performance can be monitored from remote location.
Life Cycle Management
We can take complete responsibility of product operation, maintenance, upgradation and comply latest pollution control board norms.
Comply Pollution Norms
Our design philosophy and documentation is in line with quidelines set by legal authorities. We provide support to take required approvals from pollution department
Awetech Works – The Leading Solution Provider of Effluent Treatment Plant (ETP) for Oil and Gas Industry
Our Design Philosophy
Analyze & Inspect
"You cannot improve those things
which you can not evaluate”.
✓ Analyze Water or Waste Water
Parameters.
✓ Inspect site to check availability of
Space and utilities.
Understand Application
Our Sales professionals will take detailed note of your requirement & challenges. Factors like Future expansions, end use of Water and Water depletion rate plays a very important role product designing.
Technology Selection
" Wrong selection may save you some penny initially but take out far more during operation & maintenance”. Thus, technology selection considering the soaring prices of Electricity, Manpower, Space, chemical and consumables is essential.
Design & Manufacturing
As a standard procedure we first make to-the-scale 3D design of entire project with plumbing and other connections. After discussing it with client we starts manufacturing tailor made unit in our state-of-the-art facility.
Quality Inspection
Our Ever plant has to go through the stringent Quality test, where we test the strength of fabrication, Anti Corrosion coating, Dimensions, Water leakage test and product finishing.
ENQUIRE NOW
Served Locations
-
Uttar Pradesh (UP):
Kanpur; Lucknow; Ghaziabad; Agra; Varanasi & more… -
Madhya Pradesh (MP):
Indore; Bhopal; Jabalpur; Gwalior; Ujjain & more… -
Rajasthan:
Jaipur; Jodhpur; Kota; Bikaner; Ajmer & more… -
Jammu and Kashmir (J&K):
Srinagar; Jammu -
Gujarat:
Ahmedabad; Surat; Vadodara; Rajkot; Bhavnagar & more… -
Punjab:
Ludhiana; Amritsar; Jalandhar; Patiala; Bathinda & more… -
Delhi National Capital Region (NCR):
Delhi; Gurgaon (Gurugram); Noida; Faridabad; Ghaziabad & more… -
Maharashtra:
Mumbai; Pune; Nagpur; Thane; Nashik & more…